Reservoir dam geomembrane
Short Description:
- Geomembranes used for reservoir dams are made of polymer materials, mainly polyethylene (PE), polyvinyl chloride (PVC), etc. These materials have extremely low water permeability and can effectively prevent water from permeating. For example, polyethylene geomembrane is produced through the polymerization reaction of ethylene, and its molecular structure is so compact that water molecules can hardly pass through it.
- Geomembranes used for reservoir dams are made of polymer materials, mainly polyethylene (PE), polyvinyl chloride (PVC), etc. These materials have extremely low water permeability and can effectively prevent water from permeating. For example, polyethylene geomembrane is produced through the polymerization reaction of ethylene, and its molecular structure is so compact that water molecules can hardly pass through it.
1.Performance Characteristics
- Anti-seepage Performance:
This is the most crucial performance of geomembranes in the application of reservoir dams. High-quality geomembranes can have a permeability coefficient reaching 10⁻¹² - 10⁻¹³ cm/s, almost completely blocking the passage of water. Compared with the traditional clay anti-seepage layer, its anti-seepage effect is much more remarkable. For instance, under the same water head pressure, the amount of water seeping through the geomembrane is only a fraction of that through the clay anti-seepage layer. - Anti-puncture Performance:
During the use of geomembranes on reservoir dams, they may be punctured by sharp objects such as stones and branches inside the dam body. Good geomembranes have relatively high anti-puncture strength. For example, some composite geomembranes have internal fiber reinforcement layers that can effectively resist puncturing. Generally speaking, the anti-puncture strength of qualified geomembranes can reach 300 - 600N, ensuring that they will not be easily damaged in the complex environment of the dam body. - Aging Resistance:
Since reservoir dams have a long service life, geomembranes need to have good aging resistance. Anti-aging agents are added during the production process of geomembranes, enabling them to maintain stable performance for a long time under the influence of environmental factors such as ultraviolet rays and temperature changes. For example, geomembranes processed with special formulations and techniques can have a service life of 30 - 50 years outdoors. - Deformation Adaptability:
The dam will undergo certain deformations such as settlement and displacement during the water storage process. Geomembranes can adapt to such deformations without cracking. For example, they can stretch and bend to some extent along with the settlement of the dam body. Their tensile strength can generally reach 10 - 30MPa, enabling them to withstand the stress caused by the deformation of the dam body.
kness according to the needs of the project. The thickness of the geomembrane is usually 0.3mm to 2.0mm.
- Impermeability: Ensure that the geomembrane has good impermeability to prevent water in the soil from penetrating into the project.
2.Construction Key Points
- Base Treatment:
Before laying geomembranes, the base of the dam must be flat and solid. Sharp objects, weeds, loose soil and rocks on the surface of the base should be removed. For example, the flatness error of the base is generally required to be controlled within ±2cm. This can prevent the geomembrane from being scratched and ensure good contact between the geomembrane and the base so that its anti-seepage performance can be exerted. - Laying Method:
Geomembranes are usually spliced by welding or bonding. When welding, it is necessary to ensure that the welding temperature, speed and pressure are appropriate. For example, for heat-welded geomembranes, the welding temperature is generally between 200 - 300 °C, the welding speed is about 0.2 - 0.5m/min, and the welding pressure is between 0.1 - 0.3MPa to ensure the welding quality and prevent leakage problems caused by poor welding. - Peripheral Connection:
The connection of geomembranes with the dam foundation, the mountains on both sides of the dam, etc. at the periphery of the dam is very important. Generally, anchoring trenches, concrete capping, etc. will be adopted. For example, an anchoring trench with a depth of 30 - 50cm is set at the dam foundation. The edge of the geomembrane is placed in the anchoring trench and fixed with compacted soil materials or concrete to ensure that the geomembrane is tightly connected with the surrounding structures and prevent peripheral leakage.
3.Maintenance and Inspection
- Routine Maintenance:
It is necessary to regularly check whether there are damages, tears, punctures, etc. on the surface of the geomembrane. For example, during the operation period of the dam, maintenance personnel can conduct inspections once a month, focusing on checking the geomembrane in areas where the water level changes frequently and areas with relatively large dam body deformations. - Inspection Methods:
Non-destructive testing techniques can be adopted, such as the spark test method. In this method, a certain voltage is applied to the surface of the geomembrane. When there is damage to the geomembrane, sparks will be generated, so that the damaged points can be quickly located. In addition, there is also the vacuum test method. A closed space is formed between the geomembrane and the testing device, and the existence of leakage in the geomembrane is judged by observing the change in vacuum degree.
Product parameters
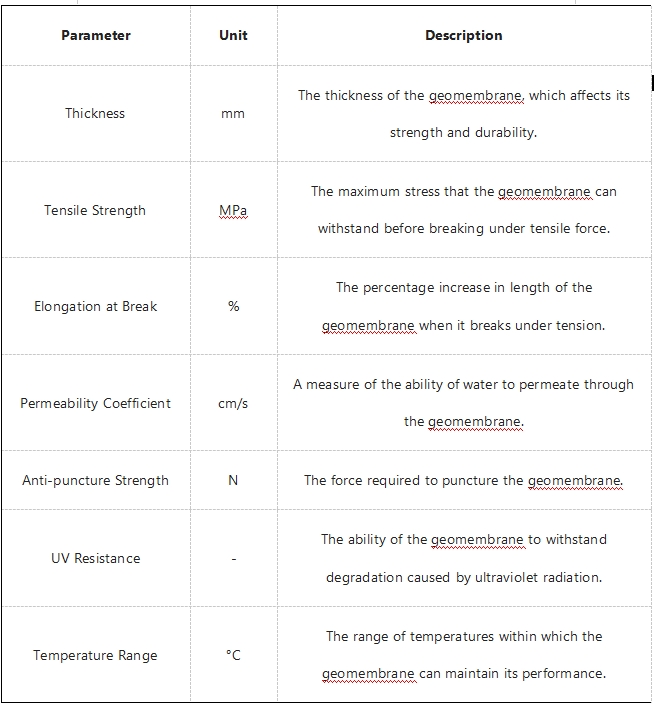